Written By: Patrick Lakin, Regional Sales Manager
How would your bottom line improve if you could make more batches per day?
Or if your batching process were made easier?
What If the quality of your products improved?
Or if your batching process were made safer for your operators?
What if you could do all of these?
A manufacturer of ice cream toppings contacted us for help with their batching process. A visit to the plant uncovered a number of issues:
- They had a powder addition system with low powder feed rates, which clogged and broke down often, took up a lot of floor space, and had a hopper 8-feet off the ground.
- They were pre-mixing cocoa powder and granulated sugar in drums, then using a hydraulic drum dumper to introduce powders to the system. This required a maintenance person to ensure the drum dumper worked throughout the process, and caused operator safety concerns.
- The system left lumps in their batch and it was difficult to clean.
- Their filling line used up a batch in 45 minutes, but it regularly took 3-4 hours to batch, so the filling line sat idle much of the day.
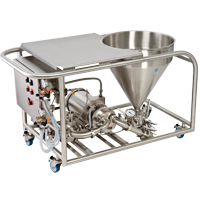
“We had our first long production run yesterday. It was fantastic!!!”
What the plant realized was, the Fastfeed:
- Used less horsepower and required less maintenance.
- Enabled them to do 5-6 batches per day and keep the filling line moving.
- Eliminated the lumps and unincorporated powders.
- Eliminated the need to pre-mix powders and, therefore, the drum dumper and the stand-by maintenance labor.
- Could be used for other products in the plant, such as pectin slurry batching.
Admix’s goal is to help our customers do things Better, Cheaper, Faster, and Safer. Ask us how we can do this for you – contact us today!